Preparation
Glow sand can be applied in a variety of ways from hand-broadcasting over fresh/wet surfaces like concrete or surface sealers and epoxies to mixed integrally in a batch of either. Before application, decide which technique you will be utilizing, and make sure you prep accordingly.
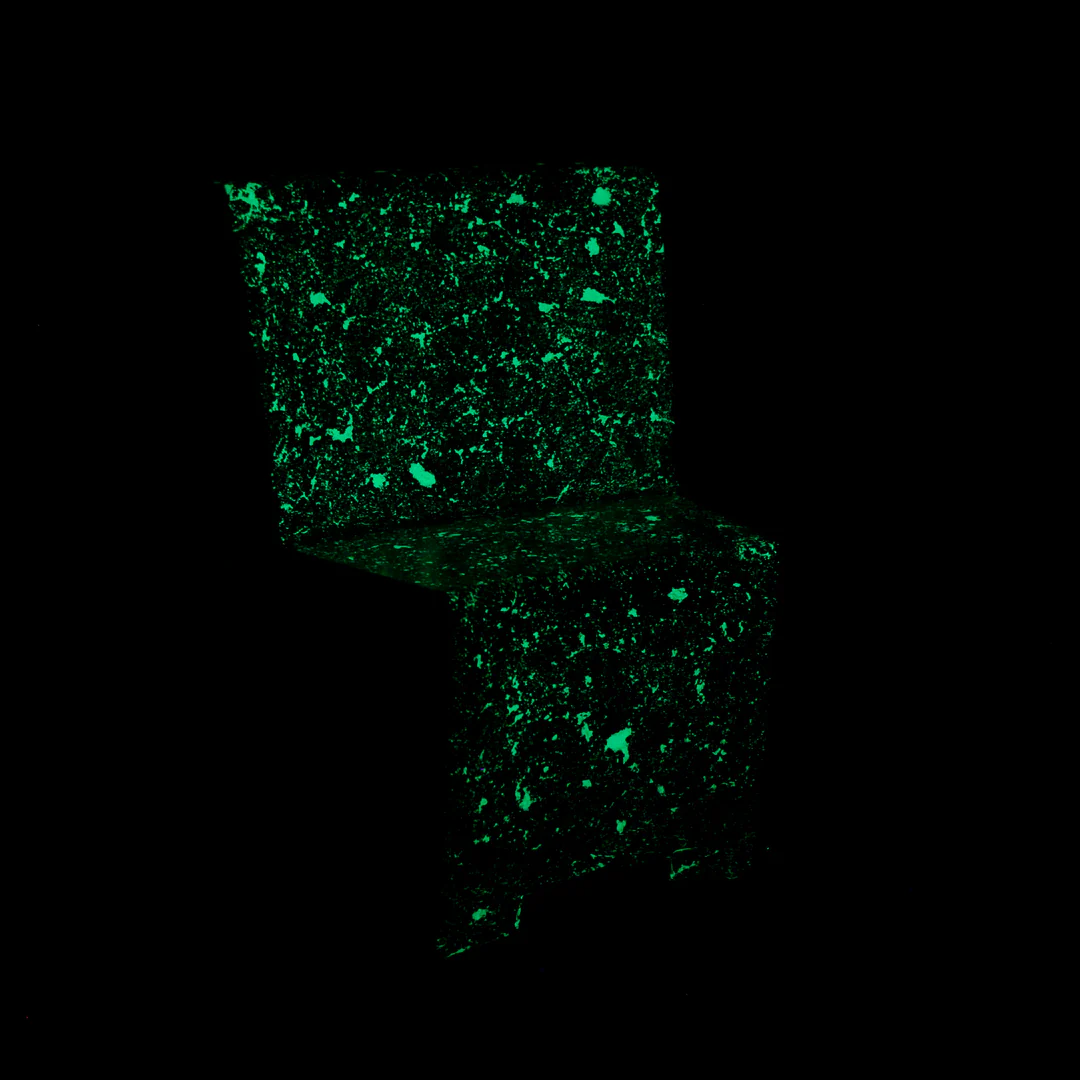
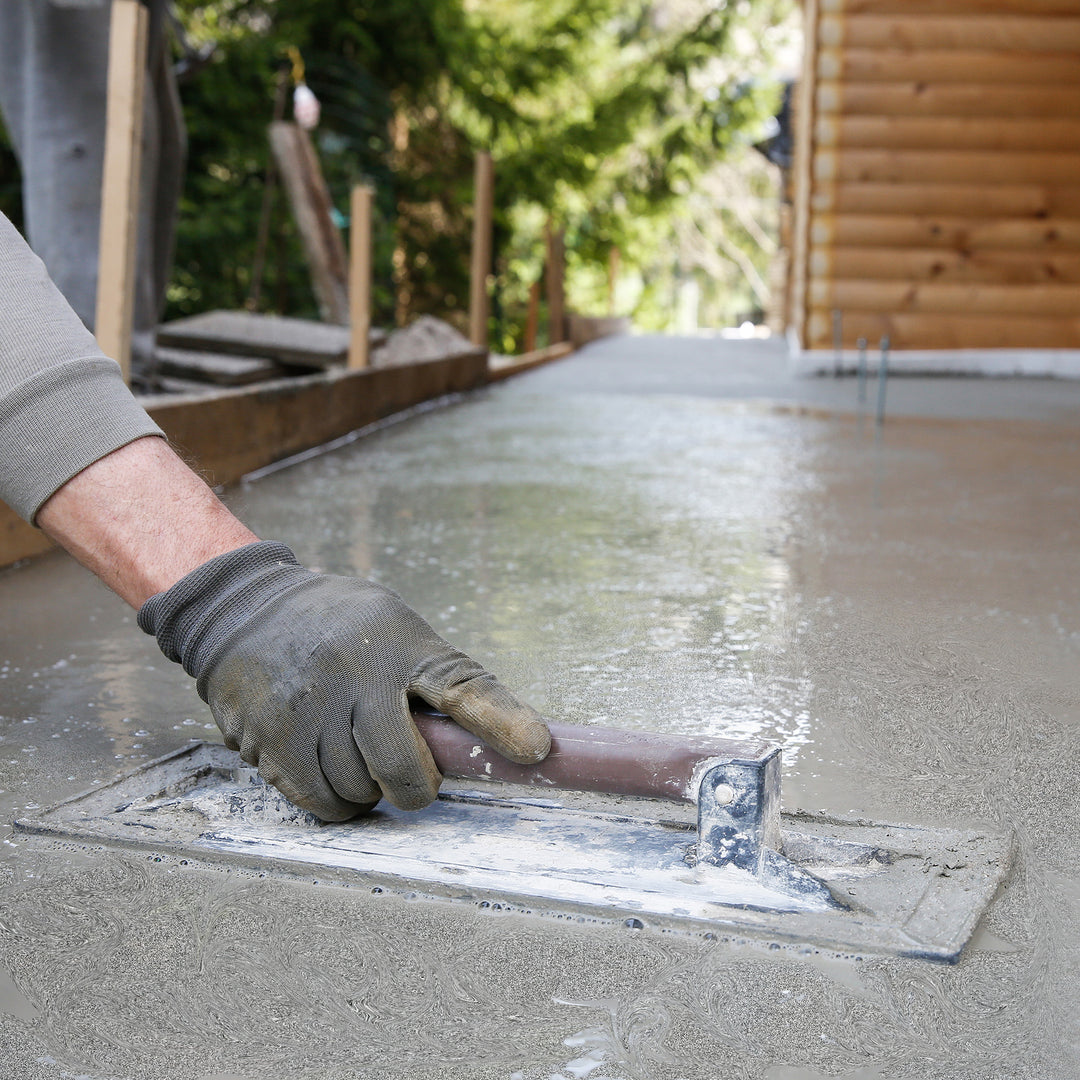
The Hand Broadcasting Technique
Consider using a Powdered Sugar Dispenser or a Restaurant-Style Salt Shaker to dispense the AGT™ glow sand evenly on top the surface. For concrete applications, hand-trowel the sand after dispensing it. These tools allow for a consistent spread over the surface, ensuring an even glow. For sealers, epoxy surfaces or concrete, apply while the coat is still wet. Once the concrete has cured, go over the surface with a Scotchbrite pad to remove the thin film formed by the evaporation of moisture.
AGT™ Glow Sand can be applied on the wet surface of darker colored concrete BUT this will require a very high loading rate to achieve the desired glow effect. A 100% coverage saturation is generally required to create a satisfactory glow effect.
The Mixing Technique
Another application method is mixing AGT™ right into the material mix. In GFRC (Glass Fiber Reinforced Concrete) and stucco applications where a compressed air hopper gun is used to apply a Face or Mist Coat, AGT™ Fine or Course glow sand is mixed right into the batch. When sprayed over the surface evenly, the glow sand creates a beautiful, uniformly glowing surface.
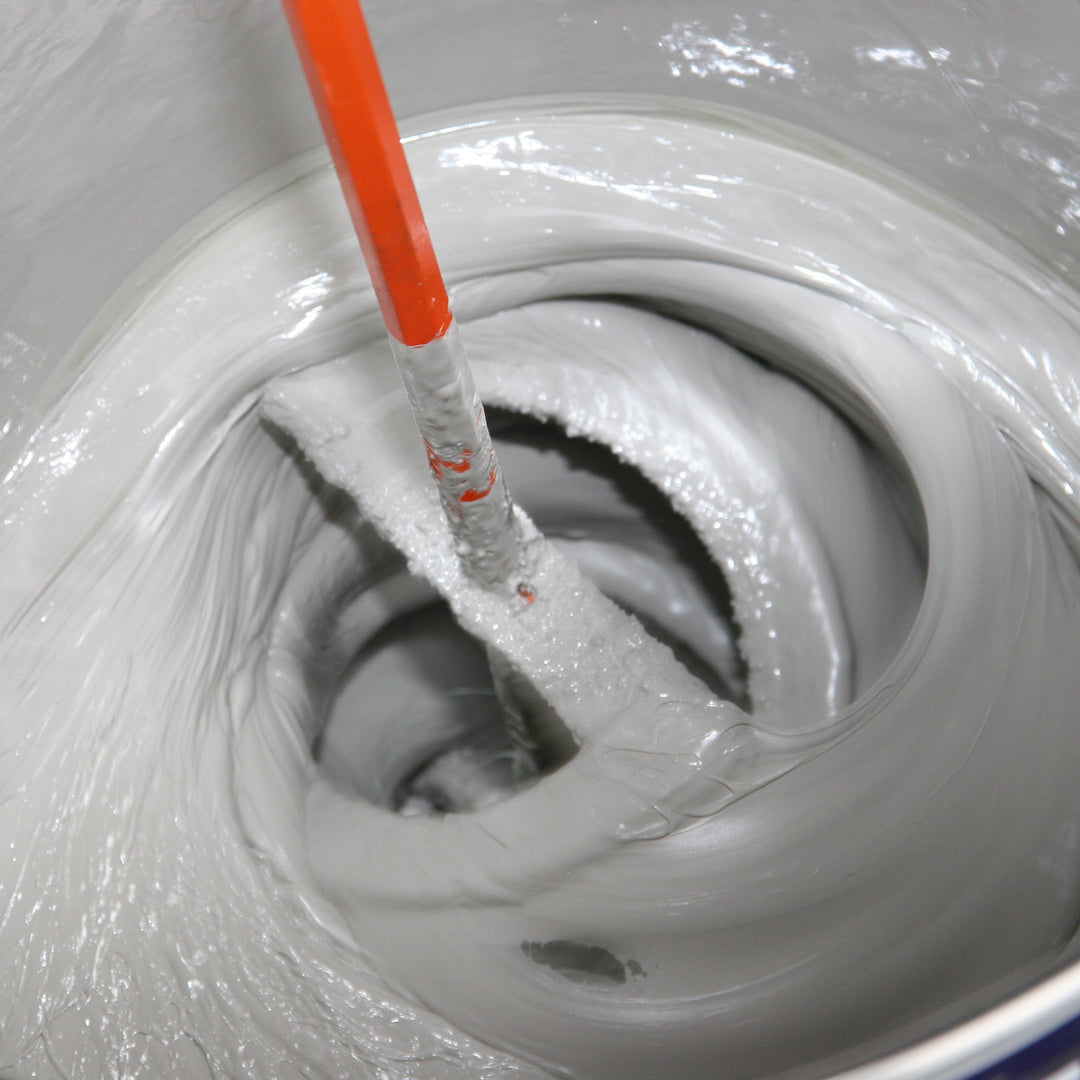
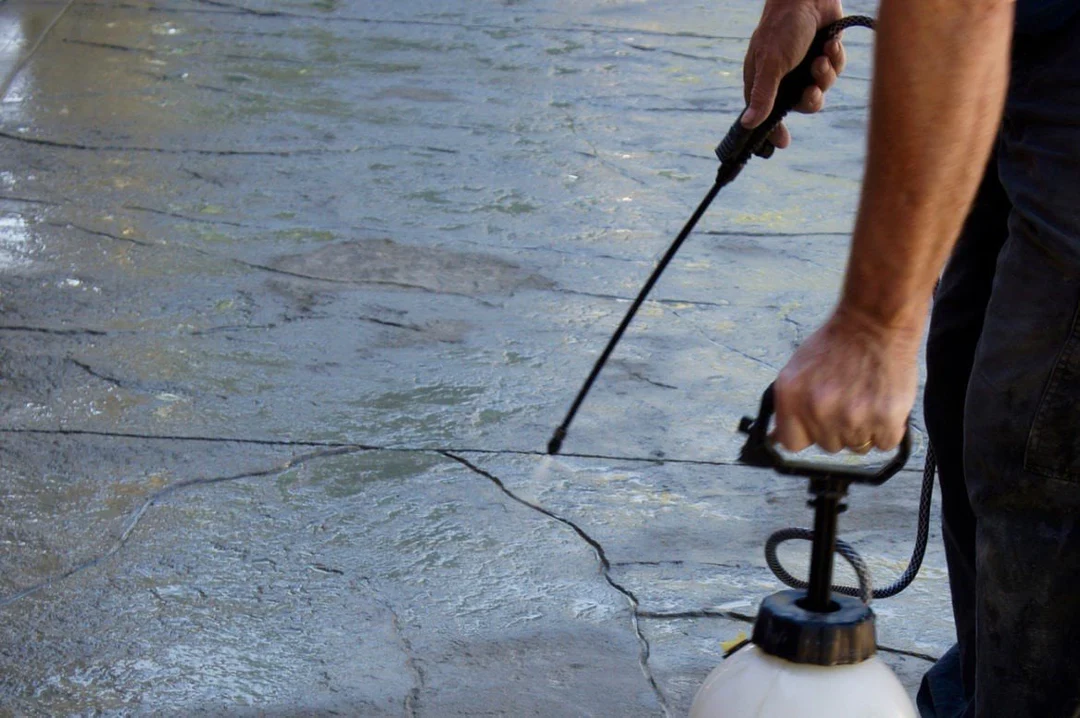
Applied in a Clear Acrylic Concrete Sealer
Add ½lb. of AGT™ Fine Glow Powder into a 3.5gal spray tank and shake well. Spray the sealer onto your cured concrete surface. Remember to keep on moving so as to not create any sealer pooling*. Once dry, apply a second coat of sealer with NO AGT™ glow sand in it. This second coat will serve to ‘lock’ the AGT™ glow sand in the surface.
Please ensure that concrete is fully cured before applying your sealer to protect against off-gas delamination. It is important to note that the glow sand will only remain intact for as long as the acrylic sealer is present. Car traffic can lead to a rapid degradation of sealer due to friction. This process will work but it is not advisable for high traffic areas. * Caution: Sealer pooling can lead to coating delamination.
Applied in Clear Epoxy & Metallics
One of the latest innovations in decorative concrete surfacing is the use of metallics in colored epoxy floor coatings. Metallics really bring the surface to the next level with a beautiful reflective property during the day. Over the past couple of years, AGT™ Fine Glow Sand has been introduced into metallic epoxy surfaces to create an otherworldly effect at night… This is achieved by broadcasting the glow sand on to the wet epoxy surface and mixed into the metallic veins. Once cured, a second coat of clear epoxy may be applied to ‘lock’ the glow sand in.
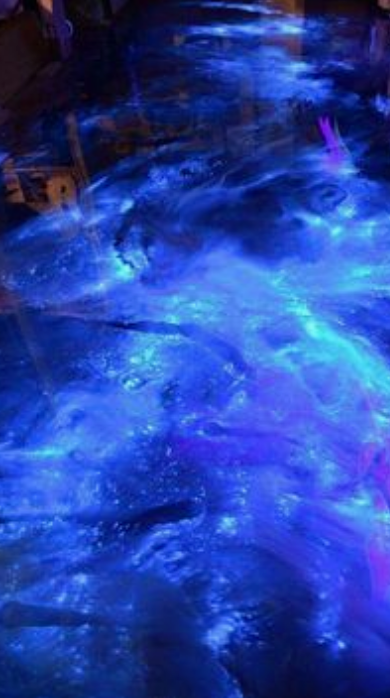
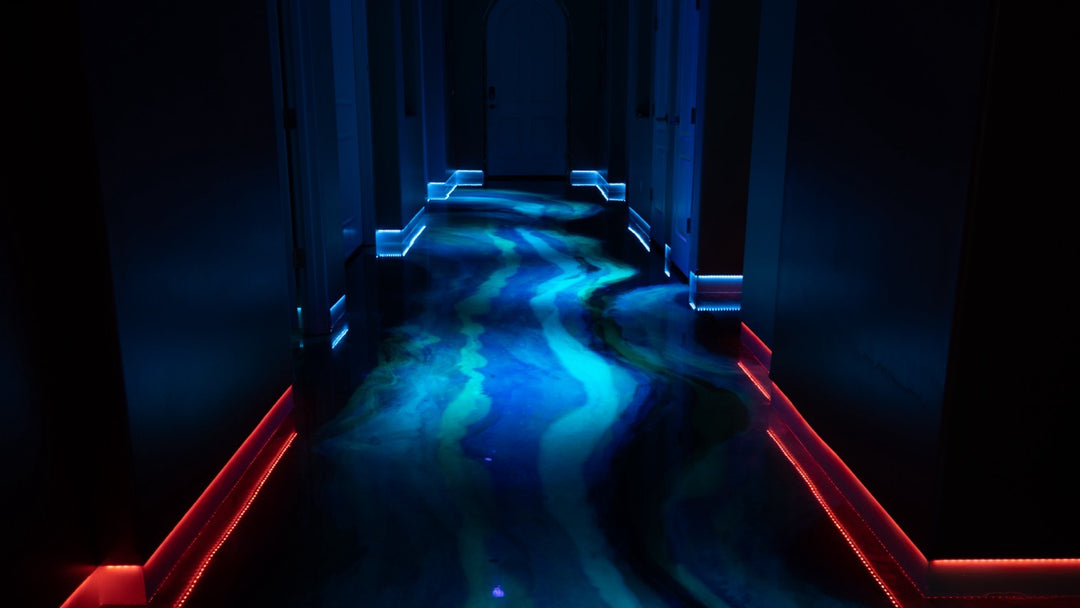
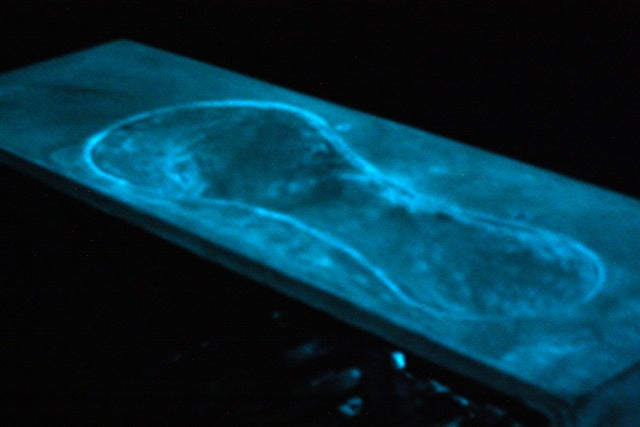
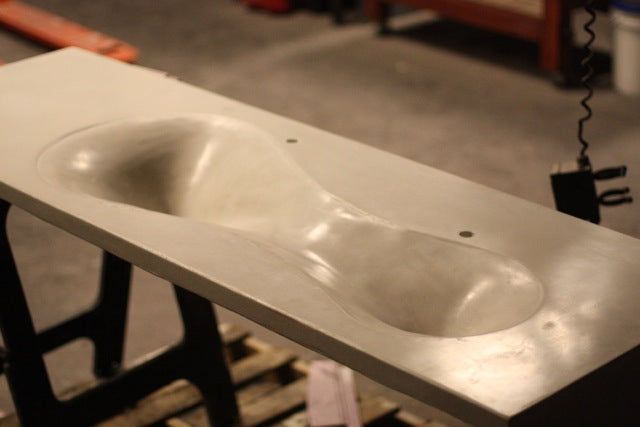
Applied in GFRC – Face Coat Mix:
AGT™ Fine Glow Sand can be mixed right into a batch of bone-colored or white Portland Cement-based GFRC (Glass Fiber Reinforced Concrete) concrete mix and then sprayed onto the Form’s surface. Once the face coat loaded with AGT™ Fine Glow Sand has been applied, a Backer Coat of concrete mixed with a high loading rate of fiberglass filaments is applied onto the surface to create the integral strength of the object you have formed.
Important to Note:
In order to arrive at the proper glow sand loading rate for your particular application, ALWAYS do some testing. This can be achieved by mixing a few micro batches of epoxy/GFRC/sealer etc. with glow sand. First weigh and measure the amount of glow sand you mixed into each batch of material - each micro-batch containing a different loading rate of glow sand.
This will help you figure out two critical metrics:
- How many (ozs/lbs.) of glow sand you will need to achieve the desired glow effect.
- How much glow sand will be required persf/m2.